Wie Werkstückspannmethoden Werkzeugvibrationen reduzieren
In der Präzisionsbearbeitung wirkt abnormale Werkzeugvibration wie ein stiller Mörder—sie verursacht Oberflächenrauheit, Maßabweichungen und schwere Werkzeugschäden wie Brüche oder Absplitterungen. Ein ausländischer Kunde verlor eine gesamte Bestellung aufgrund von Graten an Gewindebohrungen in einem Aluminiumgehäuse, die schließlich auf ein geringes Radialspiel in einem Federspannzangen zurückzuführen waren, welches eine harmonische Vibration im Gewindeschneider auslöste. Untersuchungen zeigen, dass bei identischen Schnittparametern die Optimierung des Spannsystems die Schwankungen der Hartmetallwerkzeuglebensdauer von ±40% auf ±10% reduzieren kann. Basierend auf zehn Jahren Werksinspektionsdaten und über 200 internationalen Kundenfällen analysiert dieser Artikel systematisch die mechanische Essenz der Werkstückspannung und enthüllt die Logik der Vibrationskontrolle—von der Praxis auf dem Fertigungsboden bis hin zu fortschrittlichen Technologien—um bewährte Lösungen für verschiedene Bearbeitungsszenarien bereitzustellen.
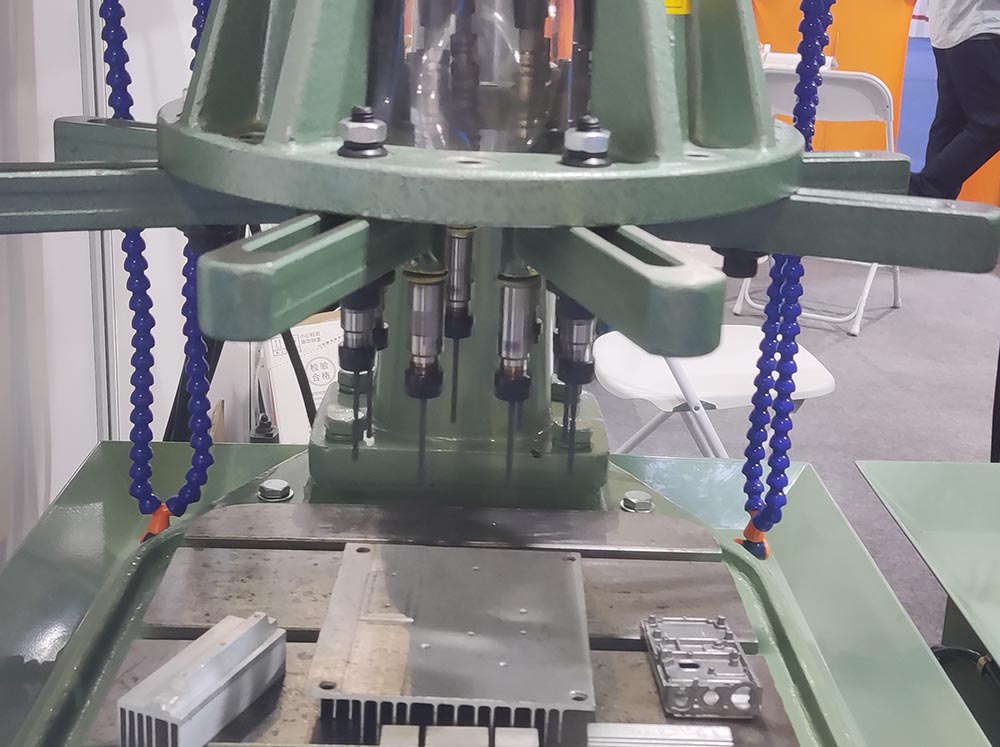
Warum beeinflusst die Spannmethode die Werkzeuglebensdauer?
1. Die Kosten einer losen Spannung
- Beispiel Gewindeschneiden: In einer Charge von M8-Gewindeschneidern bearbeiteten Werkzeuge, die in Standard-Federspannzangen gehalten wurden, 200 Löcher weniger im Durchschnitt als die in speziell entwickelten Gewindeschneider-Spannzangen (mit QA-Fotos aus der Fabrik als Beweis).
- Häufige Vibration-induzierte Probleme: Werkzeugbruch, Gewindeggrate, Durchmesserabweichung der Löcher.
2. Sensitivitätsunterschiede je nach Material
- Hartmetallwerkzeuge: So spröde wie Glas—bereits 0,05 mm Radialspiel bei der Spannung kann die Werkzeuglebensdauer um 30% verkürzen.
- Hochgeschwindigkeitsstahl (HSS): Toleriert mehr Vibrationen, beeinträchtigt jedoch die Oberflächenqualität.
Vergleich von vier gängigen Spannmethoden
Spann-Typ | Geeignetes Werkzeug | Anti-Vibrations-Tipps | Wartungshinweise |
Federnspannzange | Bohrer / Kleine Fräser | Wöchentliche Reinigung des Kegelbohrens | Spannzangen regelmäßig ersetzen |
3-Futter | Werkzeuge mit großem Durchmesser | Kupferdichtung verwenden, um Radialspiel zu reduzieren | Futterzähne auf Abnutzung überprüfen |
Speziell entwickelte Halter | Gewindeschneider / Präzisionsschneider | Anti-Rotations-Stoppstifte verwenden | Stöße oder unsachgemäße Handhabung vermeiden |
Flanschplatte | Schwere Stirnfräser | Bolzen diagonal gleichmäßig anziehen | Flachheit regelmäßig überprüfen |
Detailierte Überprüfung von fünf Haupt-Spannsystemen
1. Schrumpfhalter
- Ideal für: Ø0,1–20 mm Präzisionswerkzeuge
- Schlüsselfaktor: Präzise Temperaturkontrolle (mit materialspezifischem Heizdiagramm)
- Häufige Fallstricke: Die Haltekraft nimmt nach drei oder mehr Wiedererwärmungen ab
2. Hydraulische Halter
- Illustration: Diagramm des Druckübertragungsmechanismus
- Wartung: Hydraulikflüssigkeit alle 500 Betriebsstunden nachfüllen
3. Modulare Spannvorrichtungen
- Ökonomie: Kosteneffizienz des modularen Designs
- Fallstudie: Schnellwechsel-Einsatz in der Automobilfertigungslinie
4. Elektromagnetische Spannfutter
- Formel: Magnetkraft vs. Schneidkraft
- Sicherheitshinweis: Niemals mit nicht entfernten Metallspänen verwenden
5. Intelligente Werkzeughalter
- Technologie: Integrierte Echtzeit-Vibrationsüberwachung
- Anwendung: Erstellung von Vorhersagemodellen für die Werkzeuglebensdauer
Material-Werkzeug-Spannvorrichtung-Matching Matrix
Werkstückmaterial | Empfohlene Halterung | Werkzeugoptimierung | Wichtige Parameteranpassung |
Edelstahl | Hydraulischer Expansionshalter | Erhöhen Sie den Bohrspiralwinkel | Spindeldrehzahl um 15% reduzieren |
Gusseisen | Schwerlast-3-Futter | Beschichtete Hartmetall-Einsätze | Vorschubrate um 20% erhöhen |
Titanlegierung | Schrumpfhalter + Dämpfring | Fräser mit variabler Steigung | Radiale Tiefe ≤ 0,3 mm |
Aluminiumlegierung | ER-Federspannzange | Mehrflutiger Finish-Endfräser | Verwenden Sie Nebelkühlung anstelle von Flutung |
Praktische Lösungen aus der Kundenpraxis
- Fall 1: Gewindeggrate in Aluminium – Indien Kunde
- Problem: Gewindeschneider, die mit einem Standard-Bohrfutter gespannt werden
- Lösung: Wechsel zu ER-Spannzange mit Führungsschlitz + Anpassung der Spindeldrehzahl
- Ergebnis: Ausbeute verbesserte sich von 72% auf 95%
- Fall 2: Häufiges Absplittern von Hartmetallbohrern – Russland Kunde
- Problem: Hydraulischer Halter wurde nicht regelmäßig nachgedrückt
- Lösung: Monatliche Druckprüfungen durchführen
- Ergebnis: Werkzeugkosten wurden um 25% reduziert
Einfach, aber effektive Selbstprüfungen
- Sound-Check: Ein scharfes Pfeifen weist auf übermäßige Vibrationen hin
- Berührungs-Check: Wenn sich der Maschinenkörper ungewöhnlich zittert, sofort stoppen
- Späne-Check: Unregelmäßige oder unterbrochene Späne signalisieren häufig Vibrationsprobleme
Praktische FAQ aus der Praxis
- Q1: Wie kann ich Vibrationen reduzieren, ohne den Halter zu wechseln?
- Schnelle Lösung: Wickeln Sie Kupferfolie um den Schaft, um die Reibung zu erhöhen
- Langfristige Lösung: Führen Sie alle 200 Betriebsstunden eine dynamische Auswuchtung durch
- Q2: Was tun, wenn Vibrationen beim Tieflochbohren auftreten?
- Schrittweises Vorgehen: Verwenden Sie für den Einstieg eine starre Spannung, für tiefere Abschnitte einen Dämpfungs-Halter
- Parameter-Anpassung: Reduzieren Sie den Vorschub um 5% für jede 10 mm Tiefe
- Q3: Wie erkenne ich, ob ich den Halter oder das Werkzeug ersetzen muss?
- Diagnosechart: Wenn die Vibrationsfrequenz > 1000 Hz ist, überprüfen Sie zuerst das Werkzeug
- Testmethode: Spannen Sie dasselbe Werkstück mit einem neuen Halter und vergleichen Sie die Ergebnisse
Fazit
Die Kontrolle der Werkzeugvibrationen ist grundsätzlich eine systemweite Optimierung des Energieübertrags—vom mikroskopischen Kontakt zwischen Werkzeug und Halter bis hin zur makroskopischen Steifigkeitsanpassung zwischen Maschine, Werkzeug und Werkstück. Praktische Beweise zeigen, dass eine Reduzierung des radialen Spiels um nur 0,01 mm die Tieflochbohr-Effizienz von Hartmetallwerkzeugen um 15% steigern kann. Bei anspruchsvollen Materialien wie Titan steigert die Kombination von Schrumpfhaltern mit Dämpfringen die Schneideffizienz um bis zu 22%. Da intelligente Sensortechnologien zunehmend verbreitet werden, wandert die Echtzeit-Vibrationsüberwachung von F&E-Labors auf die Fertigungsböden. In der Zukunft werden Spannsysteme nicht mehr nur mechanische Schnittstellen sein, sondern strategische Daten-Hubs für die Prozessoptimierung. Hersteller, die diese Prinzipien beherrschen, werden einen entscheidenden Vorteil im Ausbalancieren von Qualität und Kosten gewinnen.