Warum immer mehr Hersteller von Schneidwerkzeugen umweltfreundliche Kühlmittel wählen
Im Zuge des globalen Drucks auf eine umweltfreundlichere Fertigung steht die Schneidwerkzeugindustrie vor einer doppelten Herausforderung: den verschärften CO2-Grenzsteuern der EU und den zunehmenden nationalen Umweltvorschriften. Gleichzeitig werden die versteckten Kosten und Leistungsnachteile herkömmlicher, mineralölbasierter Kühlmittel immer deutlicher. Beispielsweise zeigen Daten eines mittelständischen Schneidwerkzeugherstellers, dass M6-Gewindeschneider, die beim Bearbeiten von Gusseisenblindlöchern verwendet werden, aufgrund unzureichender Späneabführung durch herkömmliche Kühlmittel eine monatliche Bruchrate von 14 % aufweisen. Hartmetallbohrer, die unter hohen Temperaturen arbeiten, erreichen nur 65 % ihrer theoretischen Lebensdauer. Umweltfreundliche Kühlmitteltechnologie – die auf molekularer Schmierfilm- und intelligenter Wärmemanagement-Technologie beruht – definiert die Werkzeugleistung leise neu. Dieser Wandel ist mehr als eine passive Reaktion auf die Einhaltung von Umweltvorschriften; er ist eine aktive Transformation, die darauf abzielt, Kosten zu senken und die Effizienz durch technologische Upgrades zu verbessern.
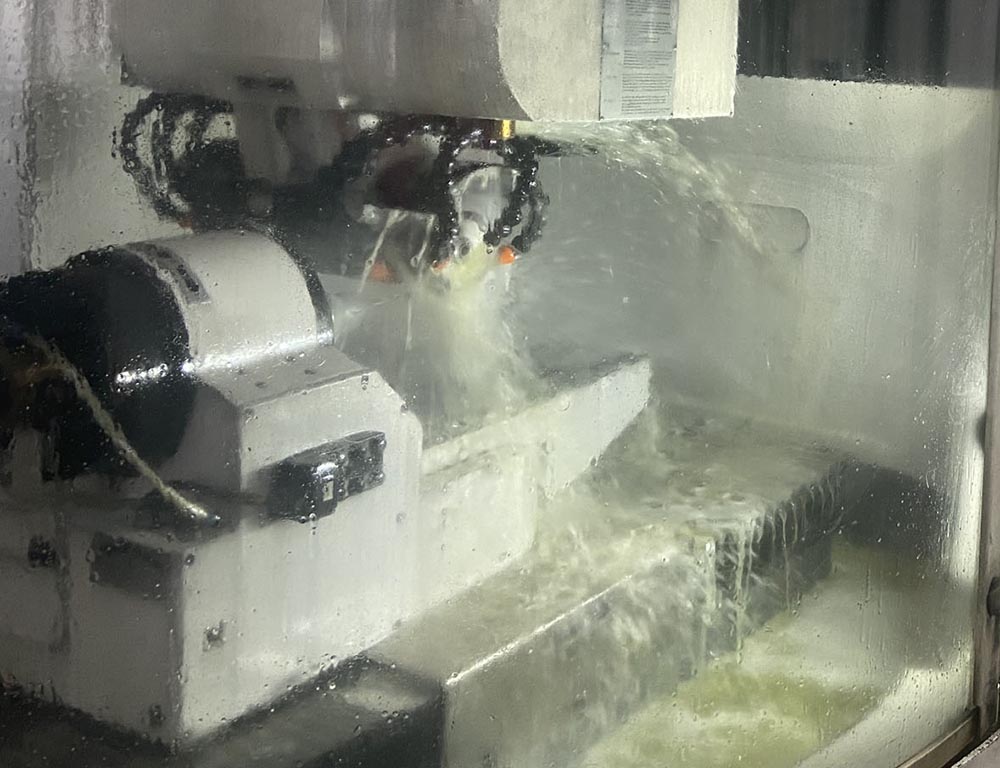
Die doppelte Herausforderung herkömmlicher Kühlmittel
1. Bearbeitungsprobleme
- Beim Bearbeiten von Gusseisenblindlöchern führen herkömmliche Kühlmittel häufig zu Spänestauungen, was die Bruchrate von M6-Gewindeschneidern erhöht. (Ein Kunde berichtete von zusätzlichen 15 verlorenen Gewindeschneidern pro Monat.)
- Beim Hochgeschwindigkeitsfräsen von Edelstahl können die Schneidkantentemperaturen 600°C überschreiten, was den Verschleiß von Hartmetallwerkzeugen beschleunigt.
2. Umweltdruck
- Neue EU-Vorschriften: Ab 2025 werden Importe von mineralölbasierten Kühlmitteln mit zusätzlichen CO2-Steuern belegt.
- Vergleich der Abwasserbehandlungskosten: Die Behandlung von Abfällen aus herkömmlichen Kühlmitteln kostet ¥3.200 mehr pro Tonne als umweltfreundliche Alternativen.
3. Die sechs verborgenen Kostenfallen herkömmlicher Kühlmittel
Kostenart | Wirkung in der Praxis | Geschätzte jährliche Verluste (kleine bis mittelgroße Betriebe) |
Abnormaler Werkzeugverschleiß | Häufige Wechsel von M8-Gewindeschneidern aufgrund von Randaufbauschneiden | ¥80.000–150.000 |
Energieverschwendung | Hohe Stromrechnungen durch überarbeitete Kühlmittelpumpen | ¥30.000–60.000 |
Umweltstrafen | Verlorene deutsche Aufträge aufgrund der Nichteinhaltung von VDI 3397 | ¥200.000+ in verpassten Bestellungen |
Gesundheit der Arbeiter | Erhöhte Krankheitsausfälle aufgrund von Hautreizungen | ¥12.000 |
Ausrüstungsrost | Reparaturen an Führungsschienen von CNC-Maschinen aufgrund von Rost | ¥25.000 |
Abfallentsorgung | Jährliche Kosten für die Einhaltung der Vorschriften zur Entsorgung von Sondermüll | ¥48.000 |
Die Kerntechnologien hinter umweltfreundlichen Kühlmitteln entschlüsseln
1. Molekularer Schutz
- Herkömmliche Mineralöle: Große Molekülketten umwickeln das Werkzeug und verhindern die Wärmeableitung.
- Pflanzliche Ester-basierte Formeln: Mikromoleküle richten sich in einer Richtung aus und bilden einen Schmierfilm von nur 0,3 μm Dicke.
2. Drei-Phasen-Temperaturregelung
Bearbeitungsphase | Kühlmechanismus | Temperaturregelungsergebnis |
Werkzeugschnitt | Nano-Blasen platzen, um die anfängliche Wärme zu entfernen | 42 % langsamere Temperaturerhöhung |
Kontinuierliches Schneiden | Phasenwechselmaterialien absorbieren latente Wärme | Stabil zwischen 480–520°C |
Werkzeugrückzug | Verdampfen des Rückstandsfilms kühlt das Werkzeug | Reduziert thermische Schockverformung |
3. Praxisnahe Testaufnahmen
- 0,8 Sekunden: Späne drehen sich in eco-Kühlmittel spiralförmig, was die Abfuhr verbessert.
- 2,3 Sekunden: Die Werkzeugspitze leuchtet blau statt rot, was auf niedrigere Oberflächentemperaturen hinweist.
Wie umweltfreundliche Kühlmittel die Lebensdauer von Werkzeugen verlängern
Vereinfachte Prinzipien:
- Ein Schutzanzug für Ihre Werkzeuge
- Pflanzliche Formeln bilden einen Reibungs-Reduzierenden Schild auf der Werkzeugoberfläche. (Labortests zeigen eine Lebensdauerverlängerung von Gewindeschneidern um 30%.)
- Ein eingebauter Kühlventilator
- Spezielle Additive beschleunigen die Wärmeabfuhr, wodurch Hartmetallbohrer vor Sprödigkeit durch übermäßige Hitze geschützt werden.
- Ein smarter Hausmeister
- Microemulsionstechnologie entfernt Späne und verhindert, dass Rückstände präzise Gewinde zerkratzen. (Ein Autohersteller berichtete von einer 22%-igen Steigerung der Gewindegängigkeit.)
Vier-Schritte-Diagnose: Benötigt Ihre Fabrik ein Kühlmittel-Upgrade?
1. Verschleiß- und Abnutzungsbewertung
- Übersteigen die monatlichen Verbrauchszahlen für Gewindeschneider/Bohrer 15 % des Einkaufsvolumens?
- Häufige Oberflächenkratzer auf den Gewinden? (Siehe visuelle Inspektionsstandards)
2. Prozessanalyse
- Hoher Anteil an tiefen Blindlöchern (Tiefe-zu-Durchmesser-Verhältnis >5)?
- Häufiges Bearbeiten schwieriger Materialien wie Edelstahl oder Titan?
3. ROI-Rechner
- Formel
Amortisationszeit (Monate) = (Nachrüstkosten + Kühlmittelkosten im ersten Jahr) ÷ (Monatliche Einsparungen bei Werkzeugen + Einsparungen bei Energie + Einsparungen bei Abfallentsorgung)
4. Checkliste zur Anbieterauswahl
- Erforderliche Zertifikate: ISO 14067 CO2-Fußabdruck
- Wichtige Dienstleistungen: Kostenlose Kompatibilitätstests für Kühlmittel
Fallstudien im Detail
- Lehren aus Misserfolgen
Fabriktyp | Erfolgreiche Praxis | Misserfolgsfalle |
Kleine Werkstatt in Zhejiang | Aufgerüstete 2 Schlüsselmaschinen | Emulsionsfehler aufgrund von Rückständen des Kühlmittels |
Mittlere Fabrik in Guangdong | Tägliche Überwachung der Kühlmittelkonzentration | 30% Überverbrauch aufgrund fehlender Schulung des Personals |
Exportorientierte Fabrik in Shandong | TÜV-Zertifizierung erhöhte Exportmarge | Pumpenfehler durch minderwertiges Filtersystem |
- Fallstudie zur realen Einsparung
- Projekt Vorher vs Nachher (Hersteller von Werkzeugen aus Guangdong)
Projekt | Vorher vs Nachher (Hersteller von Werkzeugen aus Guangdong) |
Gewindeschneiderverlust | Reduziert von 280/Monat auf 203/Monat |
Stromverbrauch | 27% Reduktion des Energieverbrauchs des Kühlmittelsystems |
Kundenaufträge | 40% Zuwachs nach Erhalt der Bosch Green Supplier Zertifizierung |
Drei häufig gestellte Fragen
- Q1: Beeinflusst umweltfreundliches Kühlmittel die Schnittgeschwindigkeit?
- A1: Keine negativen Auswirkungen. Tests an Trumpf-Maschinen zeigen eine 15%ige Steigerung der Vorschubgeschwindigkeit bei der Bearbeitung von 304 Edelstahl mit optimierten Parametern.
- Q2: Ist eine Nachrüstung der Ausrüstung erforderlich?
- A2: 80% der bestehenden Ausrüstung ist kompatibel. Es ist nur eine regelmäßige Reinigung des Ölschaltkreises erforderlich. (Ein einfaches Wartungsdiagramm ist enthalten.)
- Q3: Wird es die Kosten erhöhen?
- A3: Der anfängliche Stückpreis ist 18% höher, aber mit Einsparungen bei Werkzeugen, Abfallbehandlung und CO2-Steuern wird die Amortisation in 6–8 Monaten erreicht.
Tipps zur Implementierung für kleine und mittelgroße Betriebe
1. Schrittweise Einführung
- Phase 1: Testeinsatz bei Prozessen mit hohem Verlust (z.B. Tiefloch-Gewindeschneiden)
- Phase 2: Erstellung täglicher Kühlmittelkonzentrationsprotokolle
2. Tipps zur Auswahl von Lieferanten
- Lieferanten bevorzugen, die kostenlose Kompatibilitätstests anbieten
- Drittanbieter-Zertifizierung des CO2-Fußabdrucks verlangen
Fazit
Von Laborergebnissen bis hin zur Anwendung auf der Fertigungsebene sind die lebensdauerverlängernden Vorteile umweltfreundlicher Kühlmittel gut dokumentiert. Durch die Reduzierung von Reibung, die Regulierung der Temperatur und die Verbesserung der Späneabfuhr erreichen HSS-Gewindeschneider und Hartmetallwerkzeuge eine 25–40% längere Lebensdauer. Gleichzeitig werden Kosten für die Abfallbehandlung und Wartung der Ausrüstung reduziert. Der Erfolg erfordert jedoch die Anpassung der Lieferparameter auf die Gerätespezifikationen und die Einrichtung eines Überwachungssystems für die Kühlmittelkonzentration sowie saisonale Wartungssysteme.
Da globale Käufer zunehmend die CO2-Bilanz entlang der Lieferketten fordern, hat die Einführung umweltfreundlicher Kühlmittel sich von einem technischen Upgrade zu einer strategischen Notwendigkeit für die Exportwettbewerbsfähigkeit entwickelt. Diese scheinbar geringe Prozessverbesserung ist in Wirklichkeit ein entscheidender Wendepunkt, der nachhaltige Fertigung mit wirtschaftlichem Erfolg verknüpft und eine Zukunft mit sowohl wirtschaftlichen als auch ökologischen Gewinnen für Hersteller von Schneidwerkzeugen eröffnet.