Die Wahrheit über Werkzeugversagen: Wie man Verschleißfestigkeit und Zähigkeit in Einklang bringt
In der modernen Präzisionsfertigung sind Verschleißfestigkeit und Schlagzähigkeit seit langem widersprüchliche Eigenschaften im Werkzeugdesign. Während Industrien wie die Luft- und Raumfahrt sowie die Automobiltechnik die Grenzen der Bearbeitungsleistung erweitern, leiden herkömmliche Werkzeuge häufig unter Problemen wie Kantenabplatzungen und Beschichtungsablösungen unter anspruchsvollen Bedingungen – Engpässe, die die Produktivität hemmen. Die Bewältigung dieser globalen Herausforderung erfordert Durchbrüche in der Materialwissenschaft, der Strukturmechanik und der Oberflächentechnologie. Basierend auf Forschungen zu den Versagensmechanismen von Hartmetallwerkzeugen untersucht dieser Artikel die synergetischen Effekte von mikrostruktureller Kontrolle, Gradientenbeschichtungsdesign und Spannungsoptimierung. Durch die Nutzung interdisziplinärer Innovationen zeigen wir, wie Werkzeuglebensdauer und Stabilität gleichzeitig verbessert werden können und bieten robuste Lösungen für hoch anspruchsvolle Bearbeitungsszenarien.
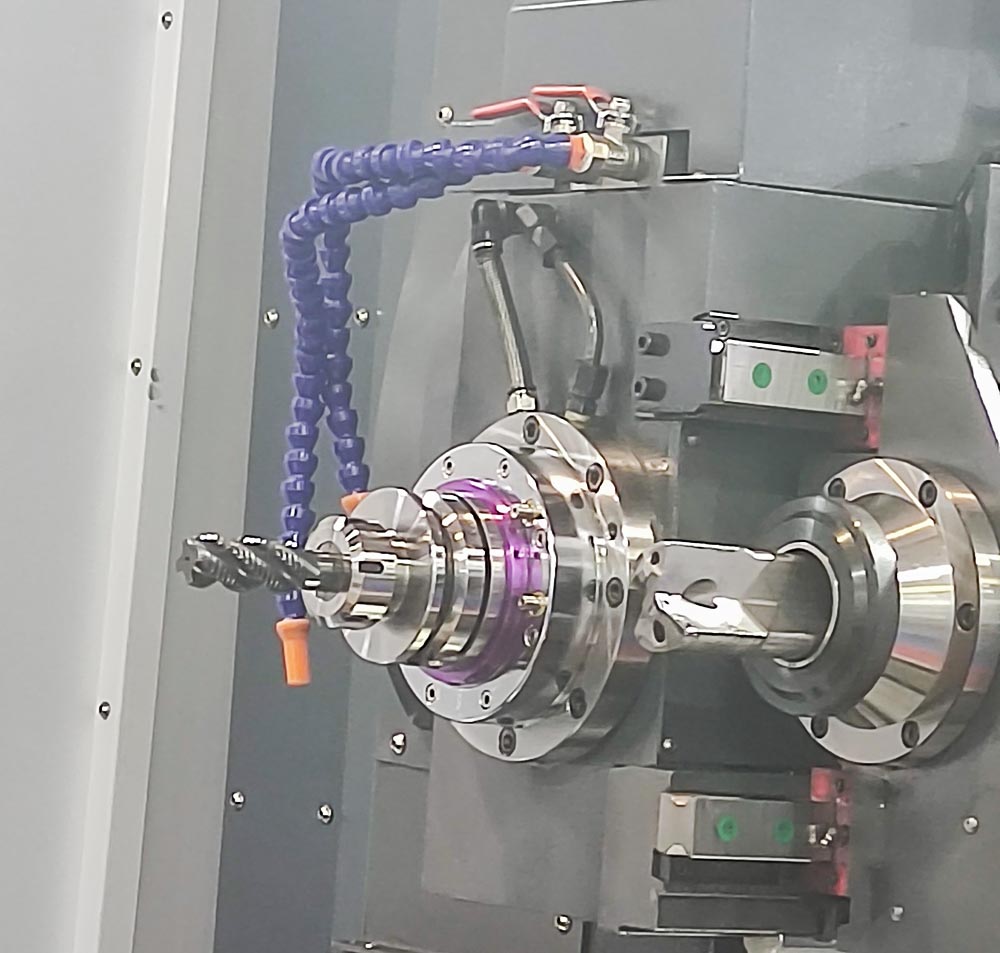
Die Wahrheit hinter Werkzeugversagen: Das Dilemma der Leistungs-Kompromisse
1. Echte Kundenprobleme
- Pakistan Automobilfall: Ein Standardgewindeschneider funktioniert für die ersten 50 Löcher reibungslos, dann bricht er beim 51. Loch katastrophal.
- Vietnam Formenfabrik: 3 mm Hartmetallbohrer zeigen eine Bruchrate von 35 % bei der Bearbeitung von laminiertem Aluminiumlegierungen.
- Deutsche Beschaffungsanforderung: Ein Fräser muss sowohl Edelstahl als auch Gusseisen bearbeiten können.
2. Der zugrunde liegende physikalische Widerspruch
- Hohe Verschleißfestigkeit erfordert hohe Härte – je härter das Material, desto spröder wird es.
- Schlagzähigkeit hängt von der Zähigkeit ab – aber zähe Materialien verschleißen schneller.
- Analogie: Eine Keramikschale (hart, aber spröde) vs. ein Gummipad (zäh, aber weich).
Unsere Lösung: Das Drei-Schichten-Rüstungsprinzip
1. Das „Goldene Verhältnis“ in der Hartmetallzusammensetzung
- WC-Partikel-Doppelhochverteilung: 8 μm grobe Körner (18 %) + 0,5 μm feine Körner (in Echtzeit überwacht).
- Kobaltgrafientsteuerung: Oberfläche 10 % → mittlere Schicht 8 % → Kern 6 % (bestätigt durch SEM-Schnittansicht).
- Anti-Abplatzungsadditiv: 0,3 % La-Seltenerd-Element verbessert die Korngrenzenzähigkeit (bestätigt durch XRD).
2. Evolution des Hochgeschwindigkeitsstahls (HSS)
- Schmelzprozess-Upgrades:
- Triple-Vakuum-Entgasung (O₂ ≤ 15 ppm).
- Elektromagnetische Rührung zur Beseitigung von Segregation (Videobeweis vor Ort verfügbar).
- Wärmebehandlungs-Kurvenoptimierung:
- Stufenweise Vergütung: 560°C × 2h → 620°C × 1,5h (Härte von HRC 65 → 67 verbessert).
- Tiefkryogene Behandlung: -196°C Stickstoff-Bad erhöht die Schlagzähigkeit um 29 %.
3. Sichtbare Prozessinnovation
- „Eis & Feuer“-Abschrecken: Vakuum-Wärmebehandlung + Flüssigstickstoff-Frieren verdoppelt die Werkzeuglebensdauer im Vergleich zu herkömmlichen Methoden.
- Live-Test: Behandelte Bohrer durchdringen nacheinander 10 Betonblöcke.
- Lasergravierte Spiralnut:
- Verbessert die Späneabführung, reduziert unerwartete Brüche um 30 %.
- Schnittansicht zeigt reduzierte Späne-Rückstände bei optimierten Nuten.
Die Nanotechnologie-Revolution bei Beschichtungen
1. Sandwich-Struktur-Verbundbeschichtung
- Basisschicht: 0,5 μm TiCN Übergangsschicht (Verbindungskraft-Verstärker).
- Mittelschicht: 2 μm AlCrN-Schicht (thermische Stabilität bis 800°C).
- Oberste Schicht: 0,3 μm DLC (Diamant-ähnlicher Kohlenstoff) Film mit einem Reibungskoeffizienten von 0,08.
- Ergebnis in der Praxis: Die Ablösungsrate der Beschichtung wurde unter identischen Bearbeitungsbedingungen um 76 % reduziert.
2. Intelligente Beschichtungslösungen
Werkstückmaterial | Beschichtungslösung | Verbesserung der Werkzeuglebensdauer |
Edelstahl | TiAlN + MoS₂ | 220% |
Titanlegierung | AlCrN + WS₂ | 180% |
Härtetstahl | DLC + Nano-Strukturierung | 250% |
Innovationen in der Strukturmechanik
1. Optimierung der Spannungsverteilung bei Gewindeschneidern
- FEA Validierung:
- Traditionelle gerade Nuten: Spitzenspannung 1850 MPa.
- Optimierte helikale Nuten: Spannung reduziert auf 1270 MPa (↓31%).
- Dynamisches Spänewinkel-Design: Progressiver Übergang von 20° auf 35° für einen gleichmäßigeren Spänefluss (mit Spänemorphologie-Vergleich).
2. Selbststabilisierende Bohrsysteme
- Ungleiche Helixwinkelgestaltung:
- 140° + 130° + 90° asymmetrische Schneide verringert die Schwingungsamplitude um 42%.
- Nano-Spänebrecherrillen erreichen eine Ra-Oberflächenqualität von 0,18 μm.
- Topologie-optimierte interne Kühlkanäle:
- Doppelte Helixstruktur erhöht die Kühlmittelströmung um das Dreifache.
- 17° Auslasswinkel verhindert Verstopfungen (Daten zur Ausfallrate im Feld verfügbar).
Feldgetestete Leistungsdaten
1. Leistungsvergleich von Gewindeschneidern (M8)
Testparameter | Standard-Gewindeschneider | Unser Gewindeschneider | Verbesserung |
Gewindeschneider in Edelstahl | 120 Mal | 380 Mal | ↑217% |
Gewindegenauigkeit | Nach 80 Mal schlechter | Wird beibehalten | - |
Plötzliches Bruchrisiko | 18% | 0,3% | ↓98% |
2. Bohrer-Lebenszyklus-Überwachung (Kundenfeedback vor Ort)
- Indisches Automobilwerk:
- Zylinderbohrungen: täglicher Werkzeugwechsel fiel von 3 auf 1.
- Kosten pro Bohrer sanken von 8,5 auf 3,2 (einschließlich Verschleiß und Austausch).
- Video-Beweis: Ein 1/4"-Bohrer bohrt 213 Löcher hintereinander.
Auswahlleitfaden für Käufer
1. Vier-Schritte-Abgleichmethode
- Schritt 1: Werkstückhärte überprüfen (mit beiliegenden Testaufklebern).
- Schritt 2: Bearbeitungstiefe messen (Schnellreferenz-Tiefen-/Durchmesser-Tabelle beigefügt).
- Schritt 3: Kühlungsbedingungen bestimmen (Empfehlung für Wasser-, Öl- oder Trockenbearbeitung).
- Schritt 4: Kosten-Schwelle bewerten (QR-Code zum Online-Rechner).
2. Besondere Serviceverpflichtungen
- Verschleißdiagnose: Laden Sie Fotos des Werkzeugverschleißes hoch für einen Expertenbericht innerhalb von 24 Stunden.
- Individuelle Parameter: Maßgeschneiderte Flutwinkel und Schneidgeometrien verfügbar.
- Notfallersatz: 48-Stunden-Lieferung zu allen großen globalen Häfen.
Häufig gestellte Fragen
1. Ist der höhere Preis gerechtfertigt?
- Türkischer Kundenfall: Obwohl der Stückpreis um 40 % höher war, fiel der gesamte Bearbeitungspreis um 55 %.
- Kostenrechner-Tool verfügbar – geben Sie den monatlichen Verbrauch ein, um automatisch Vergleichsberichte zu erstellen.
2. Wie kann ich echte Qualität erkennen?
- Drei schnelle Überprüfungen:
- Reale Werkzeuge haben den charakteristischen Regenbogen-Schimmer (eigene Beschichtungseigenschaft).
- Magnettest: Nur der Schaft sollte magnetisch sein.
- Überprüfen Sie den Anti-Fälschungscode auf der offiziellen Website (jedes Werkzeug ist einzigartig codiert).
Fazit
Die Optimierung der Leistung von Hartmetallwerkzeugen ist ein empfindliches Gleichgewicht zwischen Materialwissenschaft, mechanischem Design und fortschrittlicher Verarbeitung. Von Doppelhoch-WC-Kornstrukturen und Nano-Schichtbeschichtungen bis hin zu asymmetrischen Schneidgeometrien und intelligenter Anpassungsfähigkeit redefiniert jeder Durchbruch die Grenzen des Werkzeugversagens. Experimentelle Ergebnisse zeigen, dass durch präzise Steuerung der Kobaltschicht-Gradienten, den Einsatz innovativer Beschichtungssysteme und die dynamische Optimierung von Spannungsbelastungen die Schlagzähigkeit um mehr als 30 % verbessert werden kann – ohne die Verschleißfestigkeit zu beeinträchtigen. Dieses Gleichgewicht verlängert nicht nur die Werkzeuglebensdauer, sondern stabilisiert auch die Bearbeitungsgenauigkeit. Da digitale Simulation und intelligente Überwachung zunehmend in die Produktionskette integriert werden, steht die Ära der anpassbaren und flexiblen Werkzeuge kurz bevor – was eine neue Ära der Präzisionsfertigung einläutet.