Ein Jahrhundert der Migration in der globalen Bohrerproduktion: Der Konflikt und die Offenbarung des deutschen Ingenieurmythos und der chinesischen Smart Manufacturing Revolution
Zu Beginn des 20. Jahrhunderts, als Ingenieure im deutschen Krupp-Werk den ersten modernen Bohrer aus Wolframstahl schmiedeten, konnte kaum jemand vorhersagen, dass ein Jahrhundert später das Erbe dieses präzisen Handwerks nach Osten übergehen würde. Während der globalen Finanzkrise 2008 machte eine Branchenanekdote leise die Runde: Eine Privatfabrik in Zhejiang fertigte eine Eilbestellung von 2.000 nicht standardisierten Bohrern für einen deutschen Kunden in nur 62 Stunden – fünfmal schneller als traditionelle deutsche Hersteller. Dieser scheinbar gewöhnliche Geschäftsvorgang markierte den Auftakt zu einer globalen Machtverschiebung in der Fertigung. Deutschlands einst unangefochtene Stolz auf "handwerkliche Effizienz" sah sich nun der Herausforderung der digitalen Smart Manufacturing-Welle Chinas gegenüber. Vom Rhein bis zum Jangtse-Delta ist die hundertjährige Migration der Bohrerindustrie mehr als nur eine Neuzeichnung der globalen Produktionskarte – sie ist eine tiefgreifende Transformation technologischer Wege, Kostenstrukturen und industrieller Philosophien.
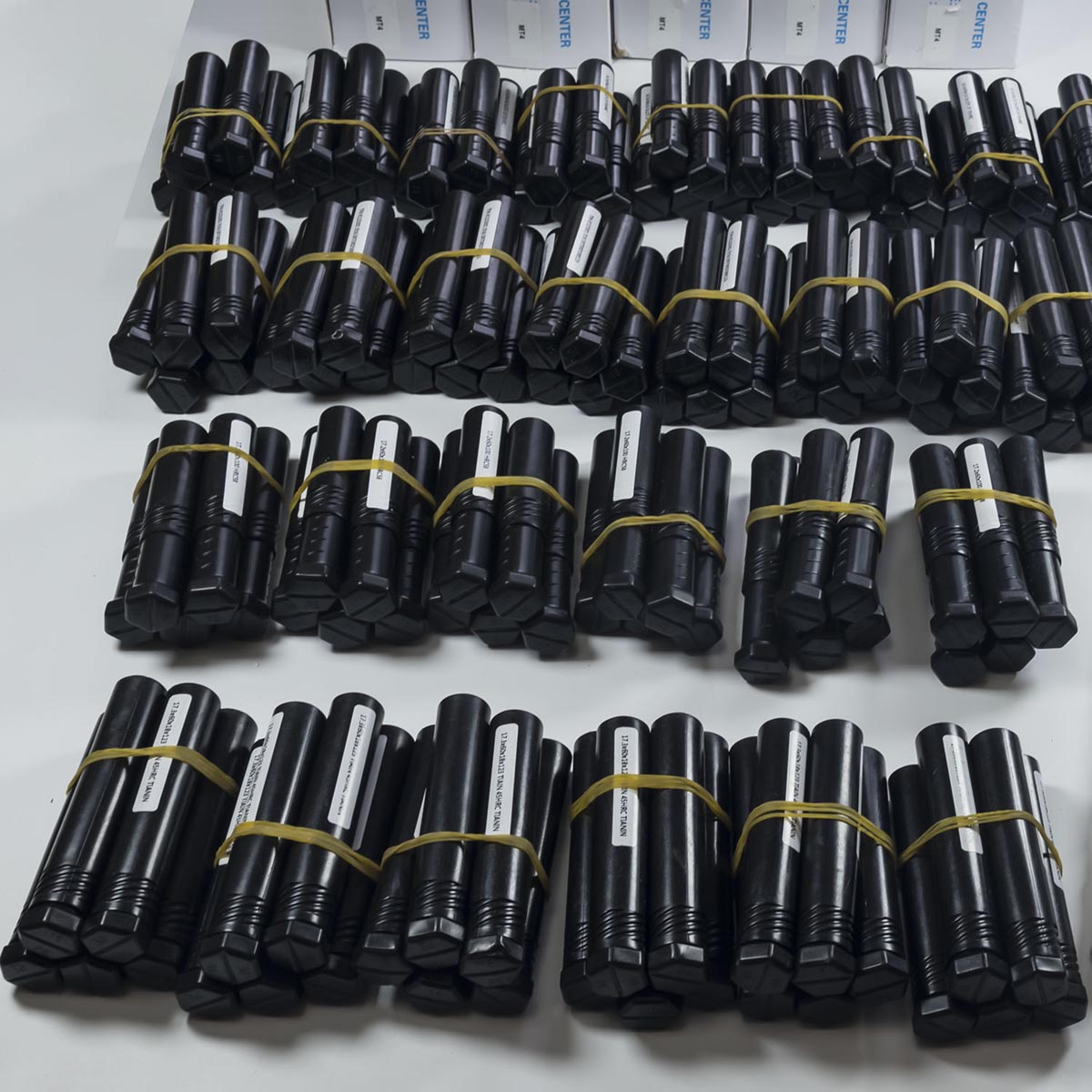
Deutsche Hegemonie: Wie präzise Fertigung geschmiedet wurde (1900–1990)
1. Ein Vorsprung in der Materialrevolution
- Durchbruch in Wolframstahl: 1914 wurde Krupp der erste, der den Wolframanteil auf 18 % erhöhte und die Lebensdauer von Bohrern verfünffachte – ein technologisches Monopol, das 30 Jahre lang anhielt.
- Getrieben durch militärische Nachfrage: Während des Zweiten Weltkriegs verbrauchten deutsche Panzerfabriken 200.000 Bohrer pro Monat, was zur Schaffung der ersten automatisierten Bohrerproduktionslinie der Welt führte.
2. Das "Hidden Champion"-Ökosystem
- Stuttgarter Industriekern: Innerhalb eines 50-km-Radius kooperierten über 300 Werkzeughersteller nahtlos – von Pulvermetallurgie bis Beschichtungsbehandlung – mit Durchlaufzeiten von nur 3 Stunden.
- DIN-Standardsystem: Der 1939 eingeführte Bohrer-Standard DIN 3409 bleibt ein globaler Qualitätsmaßstab. Chinesische Exporte wurden einst aufgrund von Toleranzabweichungen von diesem Standard vollständig abgelehnt.
3. Ein goldenes Zeitalter mit Rissen darunter
- 1995 verdienten deutsche Drehmaschinenarbeiter 35 Deutsche Mark pro Stunde (~18 €) – das 23-fache ihrer chinesischen Kollegen.
- Umweltvorschriften: Die Abwasserbehandlung für jede Tonne Bohrer erhöhte die Kosten um 1.200 €, was kleine und mittelständische Unternehmen zwang, ihre Produktion zu verlagern.
Chinas Aufstieg: Unkonventionelle Durchbrüche von der Basis (1990–2020)
1. Drei entscheidende Schlachten im technologischen Aufholprozess
- Reverse Engineering: 2001 zerlegte eine chinesische Hartmetallfabrik 200 deutsche Bohrer und entdeckte Beschichtungsdickenabweichungen von nur 0,2 μm – was zur Entwicklung eigener Beschichtungsmaschinen führte.
- Ameisentaktik: Über 300 kleine Werkstätten in Wenzhou teilten sich Produktionsaufgaben unter Verwendung von Second-Hand-Japanischen Maschinen und reduzierten die Kosten für Φ5-mm-Bohrer auf ein Drittel des Originalpreises.
- E-Commerce-Befähigung: 2015 berichtete Alibaba International von einem 400 %igen Anstieg der Anfragen für nicht standardisierte Bohrer, was es KMU ermöglichte, Bestellungen über Online-Plattformen zu erhalten.
2. Die tiefere Logik hinter den Kostenvorteilen
- Arbeitskostendividende: 2010 verdienten chinesische Formenbauer 800 RMB/Monat – nur 1/20 der Gehälter ihrer deutschen Kollegen.
- Cluster-Effekt: In Zhenjiang, Jiangsu, kürzte ein spezieller Markt für Bohrstahl die Beschaffungszeit um 3 Tage und senkte die Rohmaterialkosten im Vergleich zu Deutschland um 15 %.
3. Die Kosten der ökologischen Transformation
- 2017 zwangen Umweltauflagen in Shandong 23 Bohrerfabriken zur Aufrüstung auf PVD-Beschichtungssysteme, wobei jede Fabrik über 2 Millionen RMB investierte – doch dies half auch, den Lieferantenstatus bei BMW zu sichern.
Spitzenrivalität: Angriff und Verteidigung im Zeitalter der Smart Manufacturing (2020–Gegenwart)
1. Deutschlands Gegenoffensive: Stärkung des High-End-Marktes
- Digitale Zwillingstechnologie: MAPAL passte einen „virtuellen Bohrer“ für Mercedes-Benz an, um den Verschleiß in Echtzeit zu simulieren und die Fehler bei der Vorhersage des Werkzeugwechsels auf ±2 Stunden zu reduzieren.
- Serviceorientierte Verschiebung: Gühring führte ein "Pay-per-Hole"-Preismodell ein, bei dem 0,03 € pro Loch berechnet werden, um High-End-Kunden zu gewinnen.
2. Chinas Durchbruch: Von der Fertigung zur Smart Manufacturing
- Ultraschnelles Laser-Mikrobohren: Ein in Shenzhen ansässiges Unternehmen verwendete Femtosekundenlaser, um 500 nm Gasfilmlöcher an Bohrerspitzen zu erzeugen, wodurch die Schneidtemperaturen um 60 % gesenkt und die Lebensdauer verdreifacht wurde.
- IoT + Blockchain-Integration: Eine Dongguan-Fabrik integrierte RFID-Chips in jeden Bohrer, sodass Kunden scannen und auf vollständige Produktionsdaten zugreifen konnten, um das Vertrauen in die Produktqualität zu stärken.
3. Drittwelt-Störer
- Indiens Niedrigpreistrategie: Die Provinz Gujarat bot eine Exportsubvention von 17 % auf Bohrer an, was die Exporte nach Europa 2023 um 40 % steigerte.
- Vietnams Zollmanipulation: Erhöhte Importzölle auf Werkzeugstahl von 5 % auf 12 %, was 23 chinesische Werkzeughersteller dazu veranlasste, innerhalb von drei Jahren lokale Produktionsstätten zu errichten.
Dateninsights
- Marktanteil: Chinas Anteil an globalen Hartmetallbohrern stieg von 8 % im Jahr 2000 auf 67 % im Jahr 2023, während Deutschlands Anteil von 45 % auf 19 % fiel.
- Technologisches Aufholen: Von 2010 bis 2023 stieg Chinas Anteil an globalen Patentanmeldungen in der Bohrerbeschichtungstechnologie von 12 % auf 58 %.
Fazit
Der weltweite Wandel in der Bohrerproduktion ist ein Mikrokosmos der breiteren Entwicklung der industriellen Zivilisation. Das deutsche System der präzisen Fertigung, das über ein halbes Jahrhundert hinweg mühsam aufgebaut wurde, wird zunehmend durch die beiden Kräfte der Kosten und der Effizienz herausgefordert. Gleichzeitig zeigt Chinas Reise vom Reverse Engineering zur unabhängigen Innovation, wie Nachzügler-Nationen durch technologische Monopole hindurchbrechen können. Heute stärkt Deutschland seine Position im High-End-Markt für maßgeschneiderte Produkte, China rekonstruiert das Fertigungsökosystem mit digitaler Intelligenz und Länder wie Indien und Vietnam treten als Niedrigkostenwettbewerber auf. Die Migration ist noch lange nicht vorbei. Wenn Graphen-beschichtete Bohrer in Laborversuche eintreten und KI-Algorithmen die Werkzeugauswahl neu definieren, wird der ultimative Gewinner möglicherweise nicht durch den Aufstieg einer einzelnen Nation definiert, sondern durch denjenigen, der zuerst ein global integriertes, digital getriebenes und grünes Fertigungsparadigma aufbaut.