Fortgeschrittener Leitfaden zur visuellen Inspektion der Qualität von Gewindeschneidern: Die Drei-Schicht-Sechs-Flächen-Methode
Im Bereich der Präzisionshardware-Exporte haben Gewindeschneider—unentbehrliche Werkzeuge für die Gewindebearbeitung—direkten Einfluss auf die Montagegenauigkeit und Lebensdauer der Endprodukte. Während traditionelle Qualitätsinspektionen auf spezialisierte Instrumente angewiesen sind, erfordern Szenarien wie Exportinspektionen und Lagerstichproben oft schnelle und intuitive vor Ort Urteilsfindungsmethoden. Basierend auf den Materialeigenschaften von HSS (Hochgeschwindigkeitsstahl) und den Prinzipien der Schneidmechanik skizziert dieser Artikel systematisch ein quantifizierbares und benutzerfreundliches visuelles Inspektionssystem. Durch die Kreuzvalidierung von Glanzmerkmalen, Zahnstruktur und Montagebezügen können mehr als 90 % der häufigen Mängel innerhalb von drei Minuten aussortiert werden. Diese Methode ist besonders geeignet für Eingangsinspektionen und Zwischenkontrollen in kleinen bis mittelgroßen Exportunternehmen und adressiert effektiv die zeitlichen Einschränkungen von instrumentenbasierten Tests.
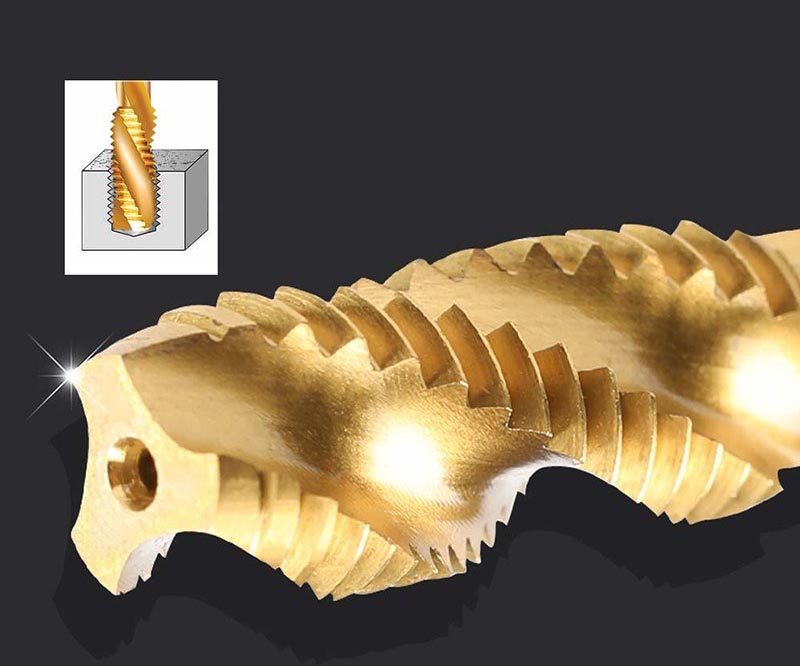
Kapitel 1: Grundlegende Materialinspektion (Drei Kernindikatoren)
1.1 Identifikation von Wärmebehandlungs-Spuren (Metallbildtechnik)
- Qualifizierte Indikatoren:
- Kratz den Schaft leicht mit einem Universalmesser; HSS-Material sollte feine, silberweiße Späne erzeugen.
- HSS-E (kobalthaltige Gewindeschneider) zeigen beim Kratzen kurzzeitig einen goldenen Reflex.
- Mängelhinweise:
- Schwarze Kratzer → Überhärten (Härtereduktion von 2–3 HRC).
- Gekrümmte Späne → Unzureichende Abschreck- und Kühlrate.
- Werkzeug-Innovation:
- Verwenden Sie ein altes Smartphone-Display als Polarisationsfilter, um die Gewindeschneiders Oberfläche zu beobachten:
- Einheitliche Streifen → Richtige Wärmebehandlung.
- Radiale Muster → Stresskonzentrationsprobleme.
1.2 Überprüfung des Beschichtungsprozesses (Alltägliche Nachweismethoden)
- TiN-Beschichtung:
- Tragen Sie Cola mit einem Wattestäbchen auf die Oberfläche auf; ein qualifiziertes Produkt zeigt innerhalb von 30 Sekunden keine Farbpenetration.
- Unter Fluoreszenzlicht sollte die Oberfläche einen gleichmäßigen champagner-goldenen Farbton zeigen.
- TiCN-Beschichtung:
- Wenn ein Magnet in die Nähe gebracht wird, zeigt ein qualifizierter Gewindeschneider eine schwache Abstoßung.
- Die Oberfläche sollte eine graphitähnliche matte Textur aufweisen.
1.3 Überprüfung der Rostschutzbehandlung (Umweltsimulationsmethode)
- Lege den Gewindeschneider quer über den Rand eines mit warmem Wasser gefüllten Glases (ohne das Wasser zu berühren).
- Decke das Glas ab und lasse es 2 Stunden ruhen.
- Qualifiziert: Keine Kondensation an der inneren Glaswand.
- Defekt: Vorhandensein von trüber Kondensation (zeigt minderwertiges Rostschutzöl an).
Kapitel 2: Tiefenanalyse der Schneidstrukturen
2.1 Spiral-Flöten-Genauigkeitsbewertung
- Einfaches Werkzeug:
- Lege den Gewindeschneider horizontal über ein Smartphone-Taschenlampenlicht:
- Hochwertig: Zeigt parallele, gleichmäßig verteilte Lichtbänder (Fehler < 0,1 mm).
- Niedrigwertig: Erzeugt wellige oder unterbrochene Lichtpunkte.
- Berührungserkennungsmethode:
- Schiebe einen Fingernagel entlang der Flöte:
- Qualifiziert: 7–9 gleichmäßige Vibrationen pro Zentimeter.
- Abnormal: Plötzliche Änderungen der Vibrationsfrequenz (zeigt Radverschleiß an).
2.2 Mikroskopische Kanteninspektion
- Bürobedarfstrick:
- Richte eine Büroklammer gerade aus, um sie als Sonde zu verwenden:
- Leichtes Tippen auf die Schneidkante vertikal; ein klares "Ding"-Geräusch zeigt Qualität an.
- Bemerkbares Ziehen beim Gleiten → Mikroabsplitterungen an der Kante.
- Faserüberprüfungsmethode:
- Fahre mit einem Kosmetikpinsel mit Baumwollfasern über den Schneidbereich:
- Qualifiziert: Fasern sind sauber abgeschnitten.
- Defekt: Fasern dehnen sich und reißen.
2.3 Schaftbearbeitungsqualität
- Papierwickeltest:
- Wickele ein A4-Blatt um den Schaft und drehe ihn:
- Hochwertig: Papier zeigt gleichmäßige Falten ohne Reißen.
- Schiefe Bearbeitung: Spiral-förmige Risse erscheinen.
Kapitel 3: Schlüsselpunkte zur Vermeidung internationaler Kundenbeschwerden
3.1 Besondere Anforderungen für EU-Bestellungen
- DIN-Standard-Details:
- Bringen Sie 3M durchsichtigen Klebeband auf dem Markierungsbereich an; ziehen Sie es fünfmal schnell ab—es sollte keine Ausbleichung auftreten.
- Der Fasenbereich sollte den Zeitungsdruck deutlich ohne Verzerrung der Schriftart widerspiegeln.
- Häufige Beschwerdebereiche:
- Leuchten Sie mit einer Smartphone-Taschenlampe in die Spanabfuhr-Rille:
- Sternartige Reflexionen → Unzureichende Politur (ein häufiges Beschwerdepunkt von deutschen Kunden).
3.2 Inspektionsfokus für den nordamerikanischen Markt
- ASME-Standardpraxis:
- Werfen Sie den Gewindeschneider senkrecht auf einen Holztisch:
- Qualifiziert: Kurzes, klares "Plopp."
- Defekt: Längerer, vibrierender Ton (zeigt interne Mikrorisse an).
- Verpackungsinspektion:
- Schütteln Sie die Verpackung in der Nähe Ihres Ohrs:
- Hochwertig: Einzelner Aufprallton.
- Niedrigwertig: Klappergeräusche (fehlgeschlagene Stoßdämpfung).
3.3 Besondere Behandlung für japanische und koreanische Bestellungen
- Lokalisierte Anpassung der JIS-Standards:
- Kratz die Oberfläche eines Seifenstücks mit einem gefrorenen Gewindeschneider:
- Hochwertig: Kontinuierliche helikale Linie.
- Defekt: Gebrochene, unterbrochene Linien (schlechte Tieftemperaturzähigkeit).
- Setzen Sie den Gewindeschneider in ein Reisfass ein und ziehen Sie ihn heraus:
- Qualifiziert: Weniger als fünf Reiskörner haften jedes Mal am Gewindeschneider.
- Defekt: Übermäßige Reiskornanhaftung (Oberflächenrauheit außerhalb der Spezifikation).
Kapitel 4: Fehlerverfolgung und Prozessverbesserung
Flussdiagramm zur Problembehandlung
Kapitel 5: Low-Cost-Präzisionsverbesserungslösungen
5.1 Modifizierte Inspektionswerkzeuge mit Bürobedarf
- Laserpointer + Winkelmesser → Spiralwinkel-Messgerät (±0,5° Genauigkeit).
- Smartphone-Makro-Linse + UV-Nagellampe → Mikroskopisches Defektbeobachtungssystem.
5.2 Lösungen zur Umweltoptimierung
- Verlegen Sie graue Acrylplatten im Inspektionsbereich (zur Verbesserung des Defektkontrasts).
- Verwenden Sie 2700K Farbtemperatur-Glühbirnen (beste Farbwiedergabeindex).
Fazit
Die vor Ort durchgeführte Qualitätsbewertung von Gewindeschneidern muss Effizienz und Präzision ausbalancieren. Die hier vorgeschlagene dreidimensionale visuelle Inspektionsmethode etabliert eine umfassende Bewertungskette—vom Mikroskopischen bis zum Makroskopischen—durch progressive Analyse der Materialglanzmerkmale, Schneidstrukturbildgebung und Validierung von Montagebezügen. Indem sie Materialwissenschaftseigenschaften innovativ in visuelle Indikatoren verwandelt, wie zum Beispiel dynamische Reflexionsbänder und Schneidenkanten-Lichtmuster, ermöglicht diese Methode es Nicht-Spezialisten, schnell die wichtigsten Qualitätsmerkmale zu erfassen. Die Praxis hat gezeigt, dass dieses System über 82 % der Probleme im Zusammenhang mit Wärmebehandlungsanomalien, Schleifdefekten und Montageabweichungen erkennt, was es besonders effektiv für Multi-Batch- und Kleinserien-Exportbestellungen macht. Durch die Integration regionsspezifischer Inspektionsmerkmale können Unternehmen das Risiko internationaler Qualitätsstreitigkeiten erheblich verringern und eine kostengünstige Qualitätskontrolllösung für Hardwarewerkzeug-Exporteure bieten.