A Century of Migration in Global Drill Bit Manufacturing: The Clash and Revelation of German Engineering Myth and China’s Smart Manufacturing Revolution
At the dawn of the 20th century, when engineers at Germany’s Krupp works forged the first modern drill bit from tungsten steel, few could have predicted that a century later, the torch of this precision craft would pass to the East. During the 2008 global financial crisis, an industry anecdote quietly made its rounds: a private factory in Zhejiang completed a rush order of 2,000 non-standard drill bits for a German client in just 62 hours—five times faster than traditional German manufacturers. This seemingly ordinary business transaction marked the opening act of a global manufacturing power shift. Germany’s once-unquestioned pride in "craftsman-like efficiency" was now facing retreat in the face of China’s digital smart manufacturing wave. From the banks of the Rhine to the Yangtze River Delta, the century-long migration of the drill bit industry is more than a redrawing of the global production map—it is a profound transformation of technological paths, cost structures, and industrial philosophies.
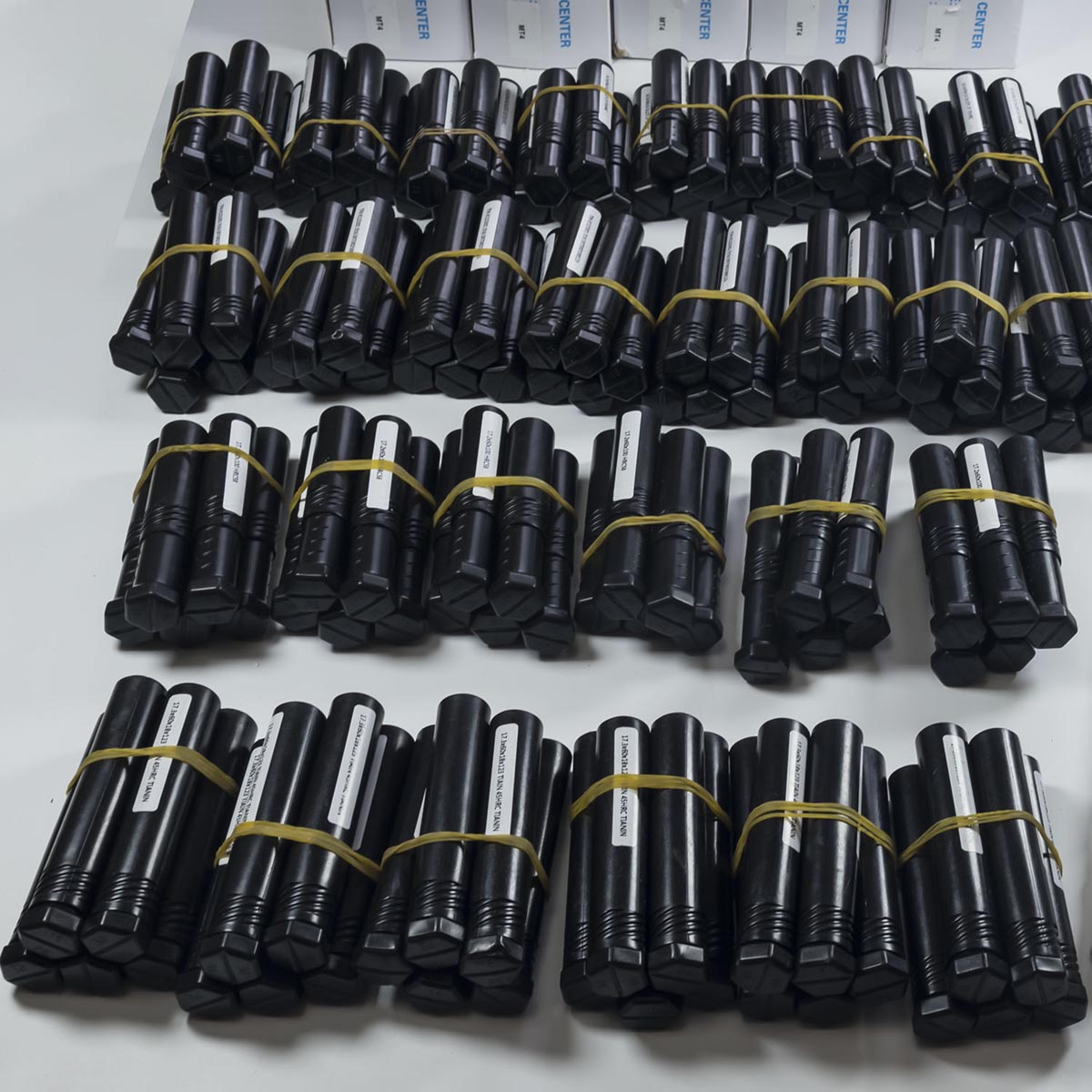
German Hegemony: How Precision Manufacturing Was Forged (1900–1990)
1. A Head Start in the Materials Revolution
- Breakthrough in Tungsten Steel: In 1914, Krupp became the first to raise tungsten content to 18%, increasing drill bit lifespan fivefold—a technological monopoly that lasted 30 years.
- Driven by Military Demand: During World War II, German tank factories consumed 200,000 drill bits per month, prompting the world’s first automated drill bit production line.
2. The “Hidden Champion” Ecosystem
- Stuttgart Industrial Cluster: Within a 50km radius, over 300 tool manufacturers collaborated seamlessly—from powder metallurgy to coating treatment—with lead times as short as 3 hours.
- DIN Standard System: The DIN 3409 drill bit standard, established in 1939, remains a global quality benchmark. Chinese exports were once rejected in full due to tolerance deviations from this standard.
3. A Golden Age with Cracks Beneath
- By 1995, German lathe workers earned 35 Deutsche Marks per hour (~€18)—23 times that of their Chinese counterparts.
- Environmental Regulations: Wastewater treatment for each ton of drill bits added €1,200 in costs, pushing small and mid-sized enterprises to relocate production.
China’s Rise: Unconventional Breakthroughs from the Grassroots (1990–2020)
1. Three Pivotal Battles in Technological Catch-Up
- Reverse Engineering: In 2001, a Chinese carbide factory dismantled 200 German drill bits, discovering coating thickness variations of just 0.2μm—leading to the development of proprietary coating equipment.
- Ant Tactics: Over 300 small workshops in Wenzhou divided production tasks using second-hand Japanese machines, cutting Φ5mm drill bit costs to one-third of the original.
- E-Commerce Empowerment: In 2015, Alibaba International reported a 400% surge in inquiries for non-standard drill bits, enabling SMEs to receive orders via online custom platforms.
2. The Deeper Logic Behind Cost Advantages
- Labor Cost Dividend: In 2010, Chinese mold technicians earned RMB 800/month—just 1/20th of their German peers.
- Cluster Effect: In Zhenjiang, Jiangsu, a dedicated market for drill bit-grade steel shortened procurement by 3 days and reduced raw material costs by 15% compared to Germany.
3. The Cost of Environmental Transformation
- In 2017, environmental crackdowns in Shandong forced 23 drill bit factories to upgrade to PVD coating systems, with each factory investing over RMB 2 million—yet this also helped secure supplier status with BMW.
Peak Rivalry: Offense and Defense in the Age of Smart Manufacturing (2020–Present)
1. Germany’s Counteroffensive: Fortifying the High-End Market
- Digital Twin Technology: MAPAL customized a “virtual drill bit” for Mercedes-Benz, simulating wear in real time and reducing tool replacement prediction errors to ±2 hours.
- Service-Oriented Shift: Gühring introduced a “pay-per-hole” pricing model, charging €0.03 per hole to lock in high-end clients.
2. China’s Breakthrough: From Manufacturing to Smart Manufacturing
- Ultra-Fast Laser Micro-Drilling: A Shenzhen-based firm used femtosecond lasers to create 500nm gas film holes at drill tips, reducing cutting temperatures by 60% and tripling lifespan.
- IoT + Blockchain Integration: A Dongguan factory embedded RFID chips into each drill bit—allowing customers to scan and access full production data, addressing trust in product quality.
3. Third-World Disruptors
- India’s Low-Cost Strategy: Gujarat Province offered a 17% export subsidy on drill bits, boosting exports to Europe by 40% in 2023.
- Vietnam’s Tariff Maneuvering: Raised import duties on tool steel from 5% to 12%, prompting 23 Chinese toolmakers to set up operations locally within three years.
Data Insights
- Market Share: China’s share of global carbide drill bits rose from 8% in 2000 to 67% in 2023, while Germany’s fell from 45% to 19%.
- Technological Catch-Up: From 2010 to 2023, China’s share of global patent filings in drill bit coating technology increased from 12% to 58%.
Conclusion
The global shift in drill bit production is a microcosm of industrial civilization's broader evolution. Germany’s precision manufacturing system, painstakingly built over half a century, is increasingly challenged by the dual forces of cost and efficiency. Meanwhile, China’s journey from reverse engineering to independent innovation reveals how latecomer nations can break through entrenched technological monopolies. Today, Germany is reinforcing its stronghold in high-end customized markets, China is reconstructing the manufacturing ecosystem with digital intelligence, and countries like India and Vietnam are emerging as low-cost contenders. The migration is far from over. As graphene-coated drill bits enter lab trials and AI algorithms redefine tooling selection, the ultimate winner may not be defined by a single nation’s rise, but by who first builds a globally integrated, digitally-driven, and green manufacturing paradigm.